The rapid growth in demand for green technologies, such as solar panels, wind turbines and energy storage technologies, e.g. Li-ion batteries, has increased the need for specialty minerals, such as graphite, lithium minerals and rare earth minerals over the past years. One of the specialty minerals, which plays a major role in the production of Li-Ion batteries as an anode material, is graphite. The graphite used in Li-Ion batteries is first concentrated from its parent rock through a beneficiation process, it is then mechanically rounded into spherical graphite, cleaned to a minimum purity of 99.95% and coated before being used as an anode material. In the course of the years, ANZAPLAN has built significant expertise in the processing of graphite raw materials into highly refined spherical anode materials. Today, ANZAPLAN is a partner of the EV supply chain active worldwide by supporting raw material companies with their process and product development efforts, who have set the goal of supplying the material base in the renewable energy sector.
One of these companies is Westwater Resources Inc (WWR), a raw material exploration and project development company headquartered in Colorado, USA. WWR conducts two graphite projects – the BAMA Mine Project and the Coosa Graphite Project – both of which are located in the graphite belt in Alabama. The goal WWR has set for themselves is the production of battery-grade graphite in the US in order to build an independent supply for the domestic industry with this strategically important raw material outside of China.
In November 2019, WWR engaged ANZAPLAN to develop the process for the manufacturing of different battery-grade graphite products: a cleaned micronized graphite (ULTRA-PMGTm), as well as a cleaned spherical graphite (ULTRA-CSPGTm). In a subsequent step, the results of the process development were transferred to the operation of a pilot plant. The goal of the pilot plant was the collection of data for the engineering of a production plant as well as the production of battery-grade products on a multi-ton scale for application testing.
ANZAPLAN took over the entire organization and execution of the pilot program of about 30 tons of the graphite concentrate based on the manufacturing procedures developed in-house.
The challenges of the setup and operation of the pilot plant (Title image) were multiple. Two examples are the installation of two large units by crane as well as the complete refitting of the ventilation system, which had to ensure the supply of fresh air.
Thanks to their highly motivated team, their meticulous conceptual design and well-prepared planning, the ANZAPLAN team was able to overcome all these hurdles and to complete the processing of the flake graphite in a tailor-made pilot plant within less than three months.
The operation of the plant was run 24/7 in a three-shift system to ensure the strict adherence to the provided schedule. The production was handled by three teams (Figure below) in 8 hour shifts with a weekly shift rotation.
The pilot program in the in-house technical center was strongly supported by Dorfner. Additionally an excellent cooperation with external technology partners (IBU-Tec and Netzsch) made the completion of this key project a real success.
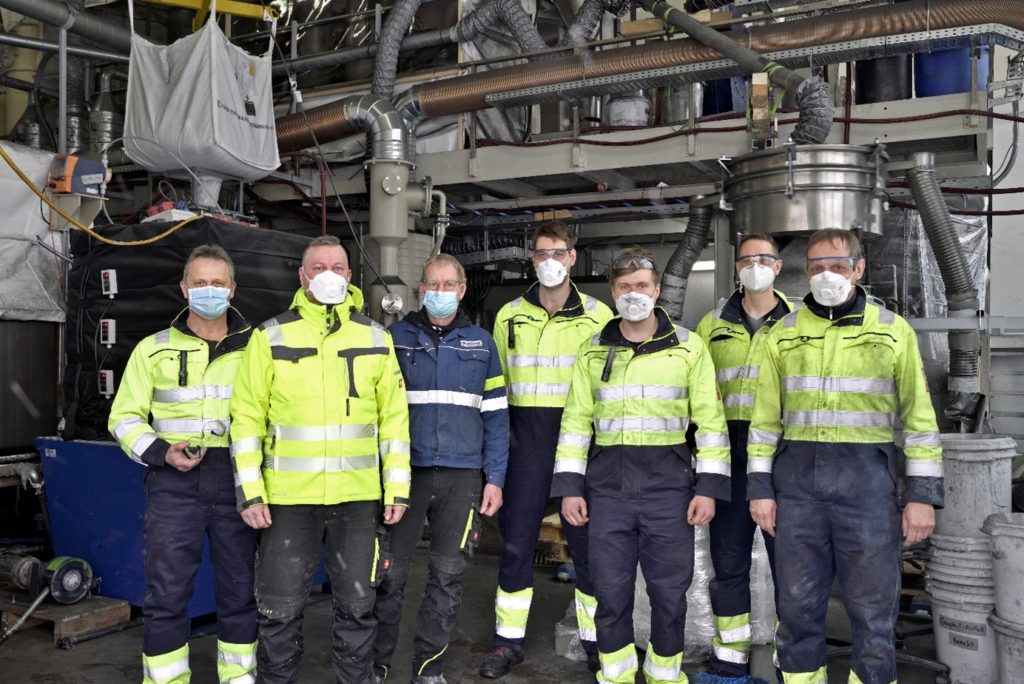
ANZAPLAN will also crucially contribute to the engineering and wastewater management to compile the final feasibility study started by WWR in February of 2021, which will take place simultaneously with the completion of the piloting phase. This is the next big milestone on the way to developing a US resource for the global graphite market and ANZAPLAN is proud to be able to participate in the successful realization of this project.
Dr. Sebastian Prinz